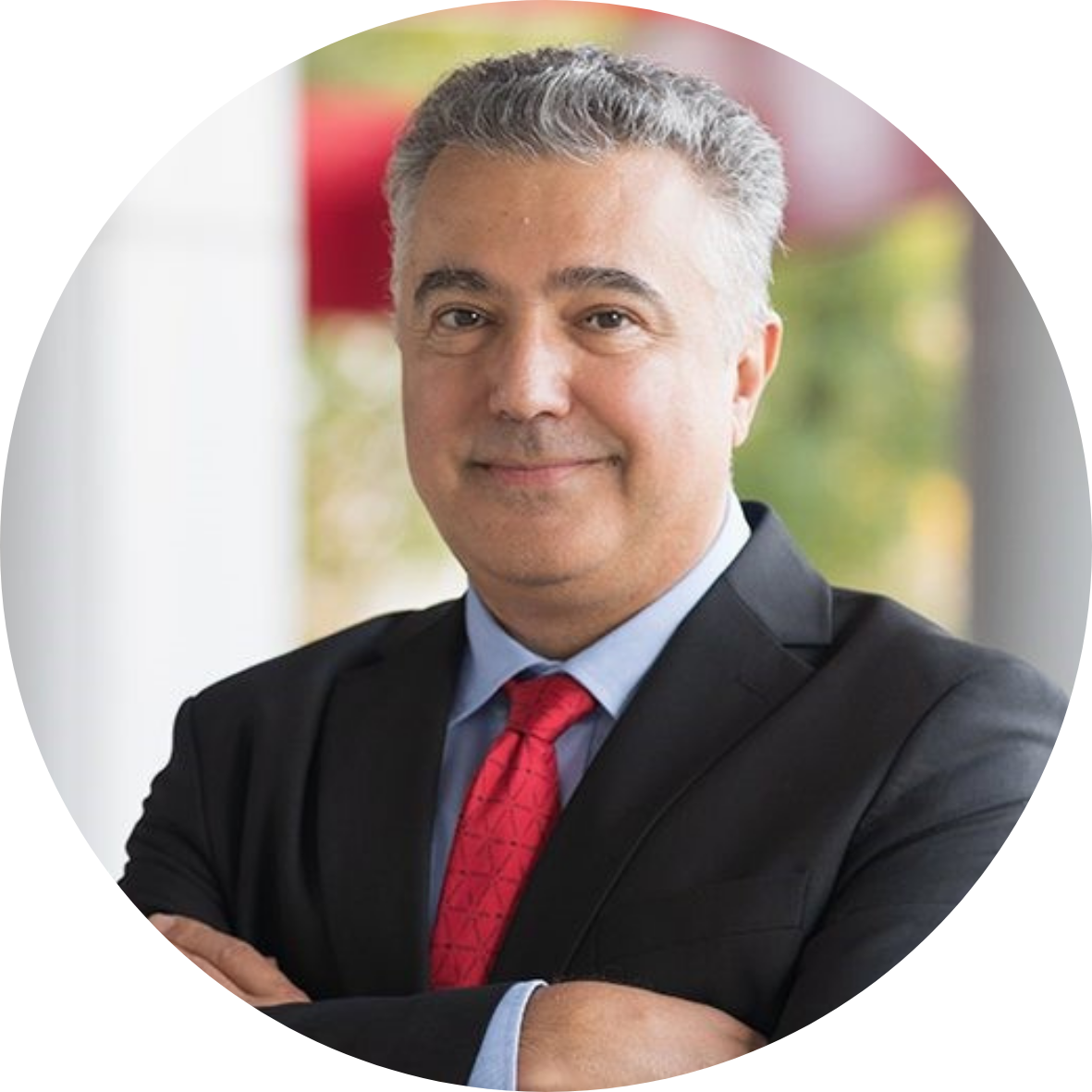
Dr. Bulent Sarlioglu is a distinguished leader in the field of electric machines, drives, and power electronics, with a career that exemplifies both technical depth and industry impact. He is currently a professor at the University of Wisconsin–Madison and serves as the Director of Technology and Collaboration at the Wisconsin Electric Machines and Power Electronics Consortium (WEMPEC), a globally recognized center of excellence.
Prior to his academic career, Dr. Sarlioglu spent over a decade at Honeywell International (2000–2011), where he played a key role in several high-profile programs—including the Airbus A380 and A350—focused on advanced electric machines and drive systems.
His pioneering work has significantly contributed to the electrification of transportation and industrial applications. He holds 22 U.S. patents and numerous international patents, and has authored or co-authored more than 300 technical publications.
Dr. Sarlioglu is deeply involved in the IEEE community, serving in leadership roles such as Vice Chair for IEEE PELS TC4, Chair of the IEEE PES Motor Subcommittee, and Chair of the IEEE IAS Transportation Systems Committee. He was honored as a Distinguished Lecturer by both the IEEE Vehicle Technology Society (2021–2024) and the IEEE Industrial Applications Society (2019–2021).
Among his many accolades, he received the IEEE Power & Energy Society Cyril Veinott Award in 2021 and the IEEE PELS Outstanding Achievement Award in Aerospace Power in 2024. He was named a Fellow of the National Academy of Inventors in 2021 and became an IEEE Fellow in 2022.
High-performance and high-efficiency electric machine design including advanced thermal management
This keynote will delve into the forefront of electric machine innovation, showcasing transformative advancements in design, materials, and manufacturing that are reshaping the field.
The first part of the talk will explore cutting-edge design methodologies that push the boundaries of efficiency and performance. Emphasis will be placed on the integration of advanced materials, including high-performance permanent magnets and novel electrical steels, as well as the growing role of additive manufacturing in enabling complex, high-precision geometries previously unattainable through conventional methods.
The second part will focus on one of the most critical enablers of power density: thermal management. Effective cooling strategies are essential not only for boosting power density but also for ensuring long-term reliability. The presentation will highlight recent breakthroughs in direct in-slot cooling and emerging cooling topologies made possible through 3D-printed heat exchangers.
Select research findings will be shared to illustrate the practical impact of these innovations, offering a forward-looking perspective on the future of high-performance electric machines.
.png?ver=9UdrjBiDAsE-jXXwcaRsmQ%3d%3d)
Masao Akiyoshi is a mechanical engineer at IHI and serves as the development manager for generators and power generation systems for aircraft. He earned his PhD from Kyoto University, focusing on the bending deformation properties of van der Waals layered materials.
Before joining IHI, he worked at Mitsubishi Electric, where he was involved in the development of high-power automotive generators, magnetic-geared generators for wind turbines, and turbine generators. Akiyoshi's primary focus is on advancing IHI's electrification-related products for aircraft, contributing to improved fuel efficiency and achieving net-zero in the aviation sector.
Development of aircraft system electrification and hybrid electric propulsion
This keynote presents overview of IHI’s R&D of aircraft and engine system electrification and technical demonstration plan. IHI is the Japanese aviation engine manufacturer and has experience on joint development of civil turbofan and total development of domestic aviation engine for defence use. System electrification technology is one of the key technology to achieve carbon neutral aviation in 2050. IHI have been developing electric system for aircraft and engine and key components such as high speed air bearing motor for light weight air machine and heat resistant motor for engine environment. Electric system which is very light and have enough safety is required for to achieve aircraft and engine system electrification. So, system level performance and safety demonstration is required. Green Innovation Fund Project proposed by IHI and supported by Japanese government plans to develop system ground test facilities to demonstrate performance and safety function of our system.
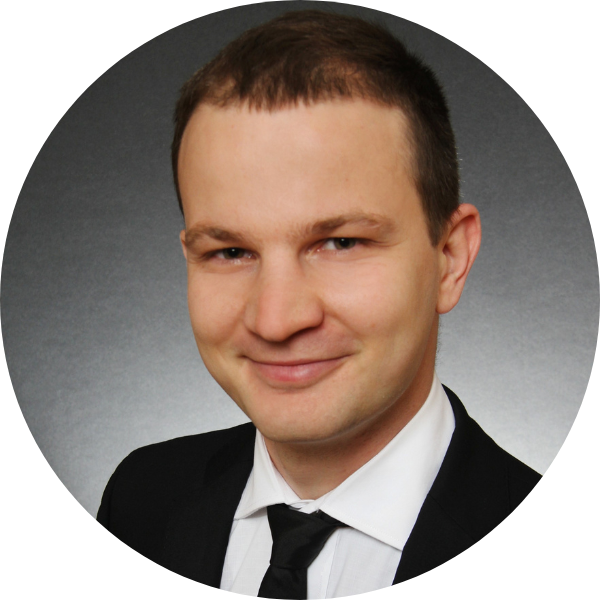
Georgi Atanasov is a researcher at the German Aerospace Center (DLR), working within the Institute of System Architectures in the Department for Aircraft Design and System Integration. He holds a Master’s degree in Aerospace Engineering from the Technical University of Munich, which he completed in 2012.
Following his studies, he spent six years supporting the Overall Aircraft Design department of the Airbus Future Projects Office as a subcontractor, focusing on conceptual and preliminary design with a particular emphasis on hybrid propulsion systems.
Since 2018, Georgi has been driving research at DLR in the field of overall aircraft design. His work is centred around sustainable aircraft concepts, with hybrid-electric propulsion continuing to play a key role in his projects.
A Radical Regional Aircraft Concept in IMOTHEP: Lessons Learned in Propulsion System Architecture and Integration
This keynote presents central insights from the development of a radical regional aircraft concept within the European Horizon 2020 project IMOTHEP, focusing on the challenges and solutions in propulsion system architecture and integration. The concept, known as REG-RAD, features a plug-in hybrid-electric powertrain and a distributed propulsion system tailored for regional missions, aiming to substantially reduce emissions while meeting realistic performance and operational requirements.
The talk describes the concept and outlines the methodological approach adopted to design and evaluate the propulsion architecture, including electric propulsion components, thermal management, and high-voltage distribution strategies. Emphasis is placed on lessons learned during the interdisciplinary collaboration between system-level aircraft modelling and detailed component studies. Special attention is given to the propulsion integration constraints, operational aspects, and the safety and reliability considerations associated with radically different propulsion systems. The retrospective analysis of the collaborative aircraft modelling process in IMOTHEP highlights key takeaways for future hybrid-electric aircraft design efforts.
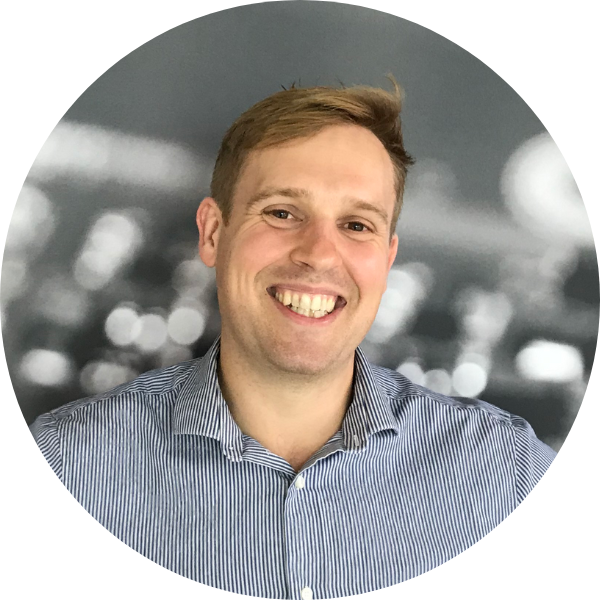
Dr Graham Bruce is a Senior Specialist Engineer at Rolls-Royce. Graham has an Meng in Electronic Engineering from the University of Manchester, and PhD in Insulation Systems for HVDC Systems. Graham has over 20 years’ industrial experience and has spent much of this time working on electrical technology and high integrity electronic products for Aerospace. His specialist experience includes power electronics, electrical hardware, and insulation coordination. Graham’s main focus is further developing the Power Electronics Product Family for Rolls-Royce’s future gas turbine product portfolio; a capability that supports more efficient power and propulsion systems for Aerospace, and the delivery of products that allow Rolls-Royce’s customers to get to net zero.
Power Electronics for an Aerospace Gas Turbine
Electrification is a key thread across the Rolls-Royce product portfolio. In Aerospace, our Engine Electronic Control Systems already provide high-integrity safety critical control and monitoring. However, we are now assessing airframer future requirements and potential product applicability for our engines in the future. One option is a "More Electric" engine where we increase the level of electrical technology content, for example extracting power directly or electrifying the oil and fuel systems. Alternatively, micro-hybridisation would enable us to optimise engine performance throughout the flight cycle to further reduce fuel consumption. Power Electronics, the ‘Solid-State Gearbox’ is at the heart of this innovation. But what does it take to deploy a Power Electronics Product Family for an Aerospace Gas Turbine.
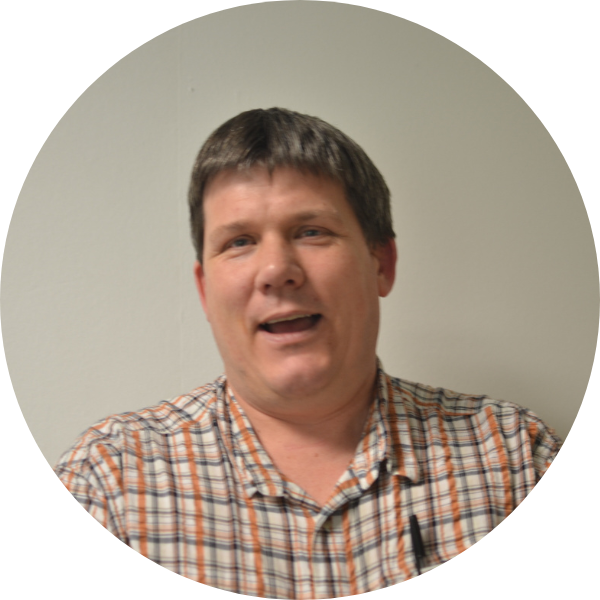
Mark Husband has a B.Eng(Hons) in Electrical and Electronic Engineering and a MSc in Electro-Magnetic Compatibility. He has worked in electrical systems for over 30 years including a number of ground breaking projects such as multi-axis automated welding systems, submarine electrical projects, type 45 electrical architecture and More-Electric & Hybrid-electric aircraft projects. In 2021 he moved from Rolls-Royce Electrical to GKN aerospace to head up the electrical network team on an ATI funded sustainable fuel cell aircraft project called H2Gear. This project is seeking to deliver the world's first large passenger full-electric aircraft. As a GKN technical associate he is responsible for ensuring the aircraft's electrical system design delivers a practical certifiable solution.
Delivering an Electrical System for Liquid Hydrogen Fuel Cell Powered Aircraft
GKN through the support of ATI funding are seeking to develop power and propulsion equipment to support the World’s first full-electric large passenger aircraft powered by liquid hydrogen fuelled fuel cells. The GKN design involves leading technology on utilising a cryogenically cooled electrical power plant. The GKN notional sustainable aircraft designs demonstrate the need for a highly integrated electrical network design to ensure all critical aircraft electrical powered loads can be supplied safely, reliably and stably across multiple flight phases. This highly integrated electrical network relies significantly on the co-ordinated operation of power electronic controlled power sources and aircraft loads to ensure optimum use of all available systems. For safety critical systems it is necessary to consider resilience against a number of potential failure events with the necessary fault detection, fault isolation and fault reaction to ensure continuous safe flight and landing (CSFL). This key note presents the holistic approach GKN have taken to deliver a safe and reliable electrical system design with a high penetration of power electronic converters.
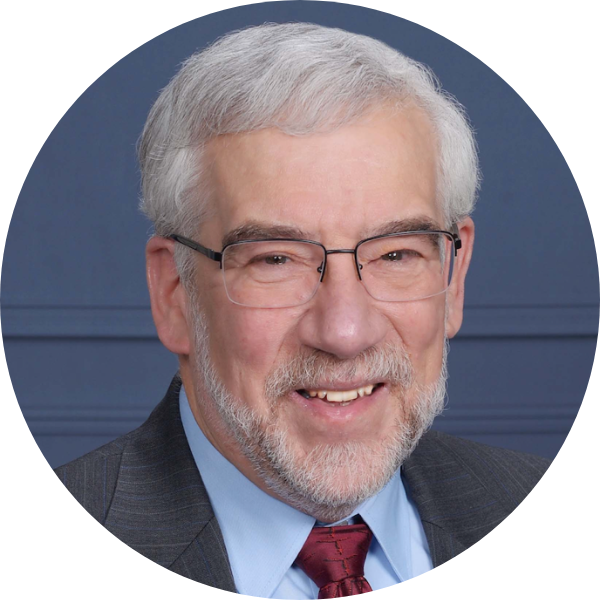
Dr. Thomas Jahns received his PhD in electrical engineering from MIT (USA) in 1978.
In 1998, Dr. Jahns joined the University of Wisconsin-Madison as a Grainger Professor of Power Electronics and Electric Machines, where he served as a Director/Co-Director of the Wisconsin Electric Machines and Power Electronics Consortium (WEMPEC) from 2007 to 2021. Prior to joining UW, he worked at GE Corporate R&D in Niskayuna, NY (USA), for 15 years. Dr. Jahns retired from the active faculty in 2021 and is now a Grainger Emeritus Professor.
Dr. Jahns received the 2005 IEEE Nikola Tesla Technical Field Award and the William Newell Award from the IEEE Power Electronics Society (PELS) in 1999. He is a PELS Past President and served on the IEEE Board of Directors (2001-2002). Dr. Jahns was elected as a member of the US National Academy of Engineering in 2015 and received the IEEE Medal in Power Engineering in 2022.
Fault Tolerant Modular Motor Drives
Impressive progress is being reported around the world on achieving major increases in the power density of electrified aircraft propulsion drive systems. However, the reliability of today’s electric machine drives falls orders of magnitude short of the daunting reliability requirements of propulsion systems in today’s commercial wide-body aircraft. While many agree that modularity will play a major role in achieving major drive reliability improvements, modularity is woefully inadequate to do the job alone. The first part of this presentation will be devoted to examining the four key features required in tomorrow’s aerospace electric machine drives to make them even candidates for meeting the highly demanding flight reliability certification requirements associated with future all-electric commercial aircraft. The second half of the presentation will address the concept of fault-tolerant modular machine drives (FT-MMDs) that is being pursued as a promising approach for achieving major improvements in the machine drive’s mean-time-to-failure (MTTF) ratings while simultaneously delivering world-class power density values. A combination of analysis and experimental results for a FT-MMD demonstrator unit now under development will be presented to illuminate both the encouraging progress being made to achieve major reliability improvements as well as the serious remaining challenges.
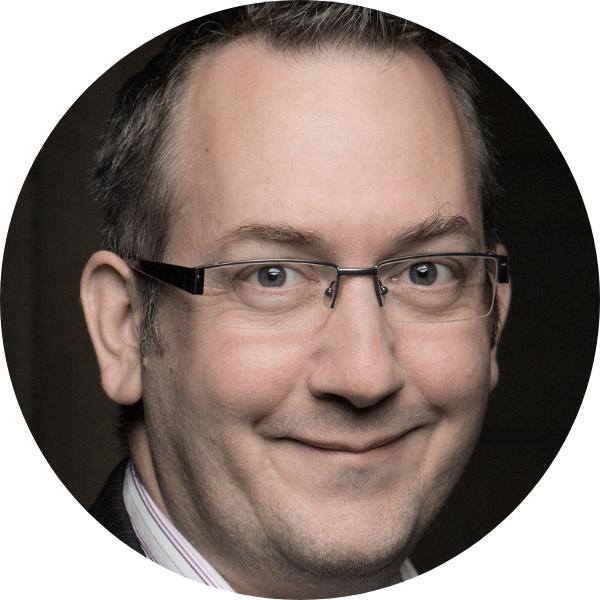
Ian Cotton is part-time Professor of High Voltage Technology at The University of Manchester and works on a range of research projects that support the transition to net-zero. He leads the University partnership with National Grid that has seen the University develop solutions including the T-Pylon overhead line and techniques to eliminate SF6 gas from the power system. He also works closely with Rolls Royce on the next generation of electrical technologies that will be used to decarbonise aircraft. In addition to his work at the University, Ian is Technical Director of aerospaceHV, a company based at Manchester Science Park that works with aerospace and automotive companies across the UK as they develop high voltage electrical systems.
Understanding The Degradation Mechanisms Of High Voltage Insulation As We Move To 1000V+
The next generation of single aisle aircraft are likely to have increased levels of electrification and the current targets suggest that operating voltages of over 1000V will be used at the DC bus level. This implies the use of insulation systems that can operate at peak-peak voltage levels in the order of at least 3000V over the lifetime of the aircraft. As such, understanding the degradation mechanism of these insulation systems is essential if the delivery of power dense yet reliable systems is the goal. This presentation will provide details of the ways in which insulation systems can be expected to fail and the test techniques that are being recommended by the standards committees to ensure that they remain fit for purpose at the end of life.
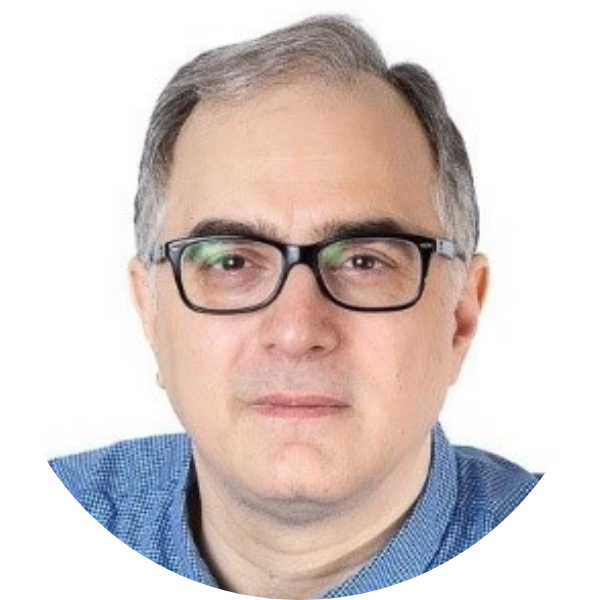
Rafael Peña Alzola earned his combined Licentiate/MSc degree in Industrial Engineering from the University of the Basque Country in Bilbao, Spain, followed by his PhD in Electrical Engineering from the National Open University (UNED) in Madrid, Spain.
He was a Guest Postdoctoral Fellow in the Department of Energy Technology at Aalborg University, Denmark, from September 2012 to July 2013. Between August 2014 and December 2016, he held a Postdoctoral Research Fellowship in the Department of Electrical and Computer Engineering at the University of British Columbia, Vancouver, Canada. From January to May 2017, he undertook a short-term industrial collaboration at the University of Alcalá in Madrid, Spain.
Since June 2017, he has been a Research Fellow at the Rolls-Royce University Technology Centre at the University of Strathclyde, Glasgow, UK. He has collaborated with several aerospace companies including Airbus, Raytheon UK, IHI Corporation and GKN. His research interests include energy storage, LCL filters, solid-state transformers, innovative control techniques, solid-state breakers and power electronics for aircraft applications.
University Perspectives on Power Electronics for Aircraft Applications
University perspectives on aircraft power electronics must address collaboration with industry and the training of future engineers.
Industry-established converters set the benchmark for academic topologies. While inexpensive and reliable silicon devices continue to reduce losses, wide-bandgap semiconductors (GaN, SiC) dominate research due to their weight and efficiency advantages. Wide-bandgap devices introduce PCB-layout complexity and require high-bandwidth sensing.
Universities rely heavily on simulation tools. Spice-based software evaluates switches and gate drivers, with a trend towards virtual prototyping on multi-domain platforms such as Modelica or VHDL-AMS. Magnetic and thermal design can benefit greatly from finite-element analysis, encouraging cross-disciplinary academic research.
Many simulation suites support automatic code generation for microcontrollers, DSPs and FPGAs, increasingly favoured for certification. Rapid controller prototyping uses real inverters or hardware-in-the-loop (HIL) systems for exhaustive testing.
In addition to reducing converter and filter size, aerospace power electronics also demand protection schemes — over-current tolerance, device-level protection and solid-state breakers. Modular, parallel-interleaved converters balance redundancy against weight and cost. Reliability monitoring hinges on online sensing and digital twins. At system level, aircraft electrical networks — where converters are now ubiquitous — must support dynamic reconfiguration under fault conditions.
Finally, teaching power electronics is challenging, given its broad scope. At Strathclyde, lectures are complemented by simulation software, educational videos and project-based learning.
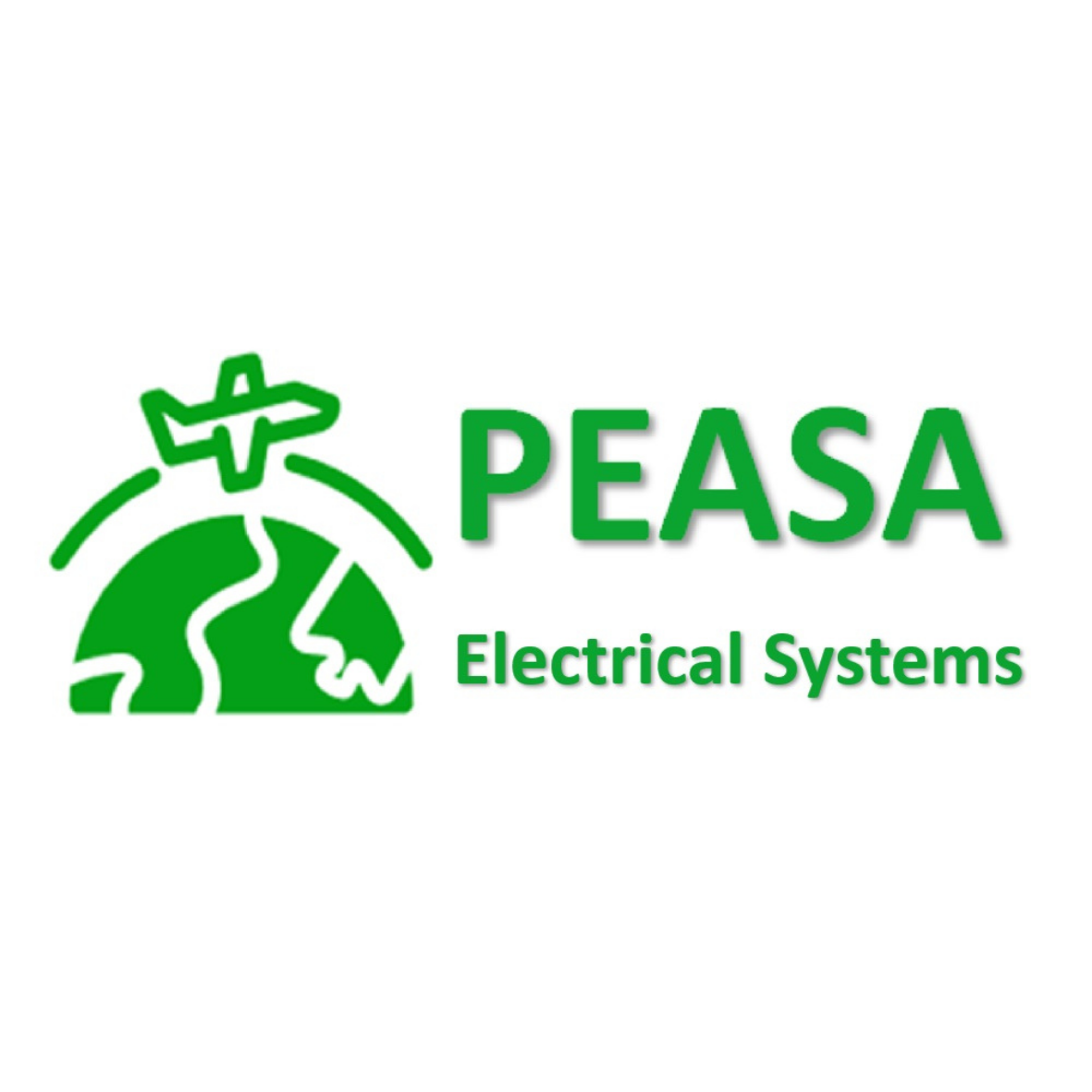
Peter Malkin has spent the majority of his career in Industrial Research on Electrical Power Systems before to moving into Academia.
Prior to his present position at Newcastle University, he was appointed Professor of Electrical Power at Cranfield University. Before that he had a career working at Rolls-Royce where he was appointed as Senior Company Fellow in Electrical Power and Chief Technologist for Electrical Systems. During this time, he had significant involvement with the Power Optimised Aircraft (MEA) programme with Airbus and with the development of the electrical power systems on the Boeing 787 Dreamliner aircraft. In addition, he has had a long interest in the application of Cryogenic and superconducting technologies.
Electric Power Systems in Large Aircraft - an Overview
Current large aircraft (over 100 seats) have used essentially the same technology since the 1950s. This may be described as Twin Turbofans (High Bypass) mounted underwing on a tube and wing aircraft. Clearly this technology has evolved over time, resulting in significant gains in efficiency but whilst highly sophisticated, the technology has reached the end of its development curve meaning further gains are small and very difficult.
During this period the industry has investigated the potential use of electric power systems both to improve performance of existing technology and even to replace it. However, the specifics of this application requiring exceptionally high-power density along with very high reliability have proved extremely challenging.
Nevertheless, over the last thirty years or so the industry has investigated the following.
1 Auxiliary Power
2 More Electric Aircraft
3 Hybrid Assisted Power
4 Full Electric Propulsion
Each of these will be described in the presentation and the options going forward facing the industry, particularly given the growing environmental pressures against the background of significant growth in demand for air travel Worldwide.
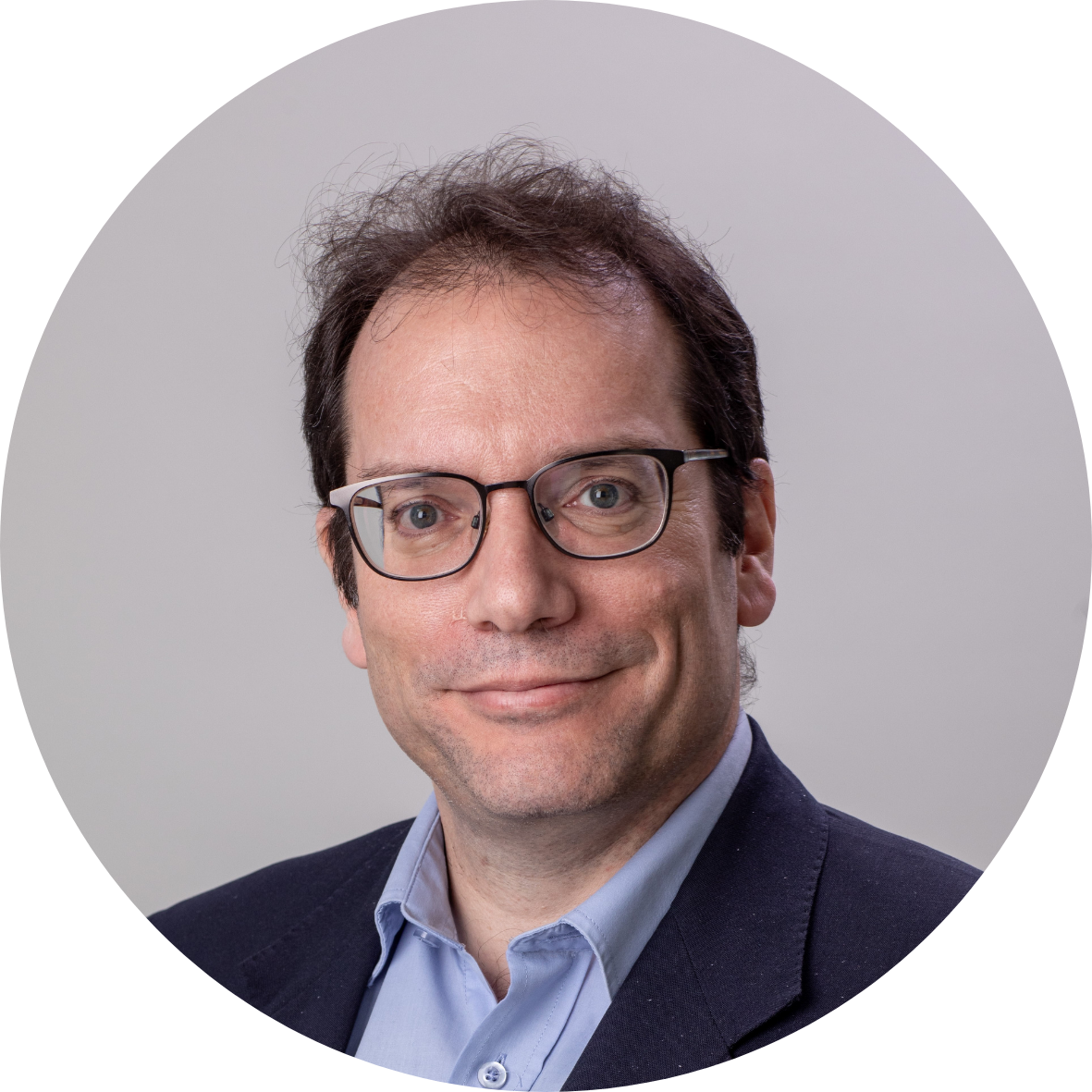
Giovanni Raimondi (Joe) has an MA in Engineering Science from Cambridge University and an MSc in Control Systems and a PhD in control of single-axis and multi-axis electrical drives from Sheffield University. After working at Sheffield University as a Research Associate, including an electrical flight control demonstration project with Lucas Aerospace, and at Dyson Research Ltd on domestic appliance drivetrains he joined TRW (now Safran) in 2000. He has since held various project, functional and leadership roles including defining and guiding significant Safran technology investment as Director of UK R&T programmes. Joe is currently Machines & Drive Systems Technical Director, responsible for engineering teams in the UK and France, and is a Safran Group Distinguished Expert in electrical systems.
Network Conversion Challenges
Safran's strategic decision to bring together electrical power capabilities and technologies developed within the group and obtained through acquisition has enabled a significant understanding of the complexities and implications of large-scale power conversion within aircraft systems. Electrical power opens the door to new air mobility applications and promises to facilitate decarbonisation of existing air transport applications as has already been widely demonstrated in the automotive and other segments. Other than the obvious challenges of “paying their way”, the power conversion equipment design and integration has to overcome some significant obstacles before the potential benefits of electrification can be realised. Air travel is the safest form of transport today, so it is essential for robust validation of the safe operation of new high-power electrical equipment and systems. This is particularly challenging in the context of pioneering forms of air vehicle such as multi-rotor eVTOL aircraft, but the bar is also extremely high for more familiar fixed and rotary wing applications.
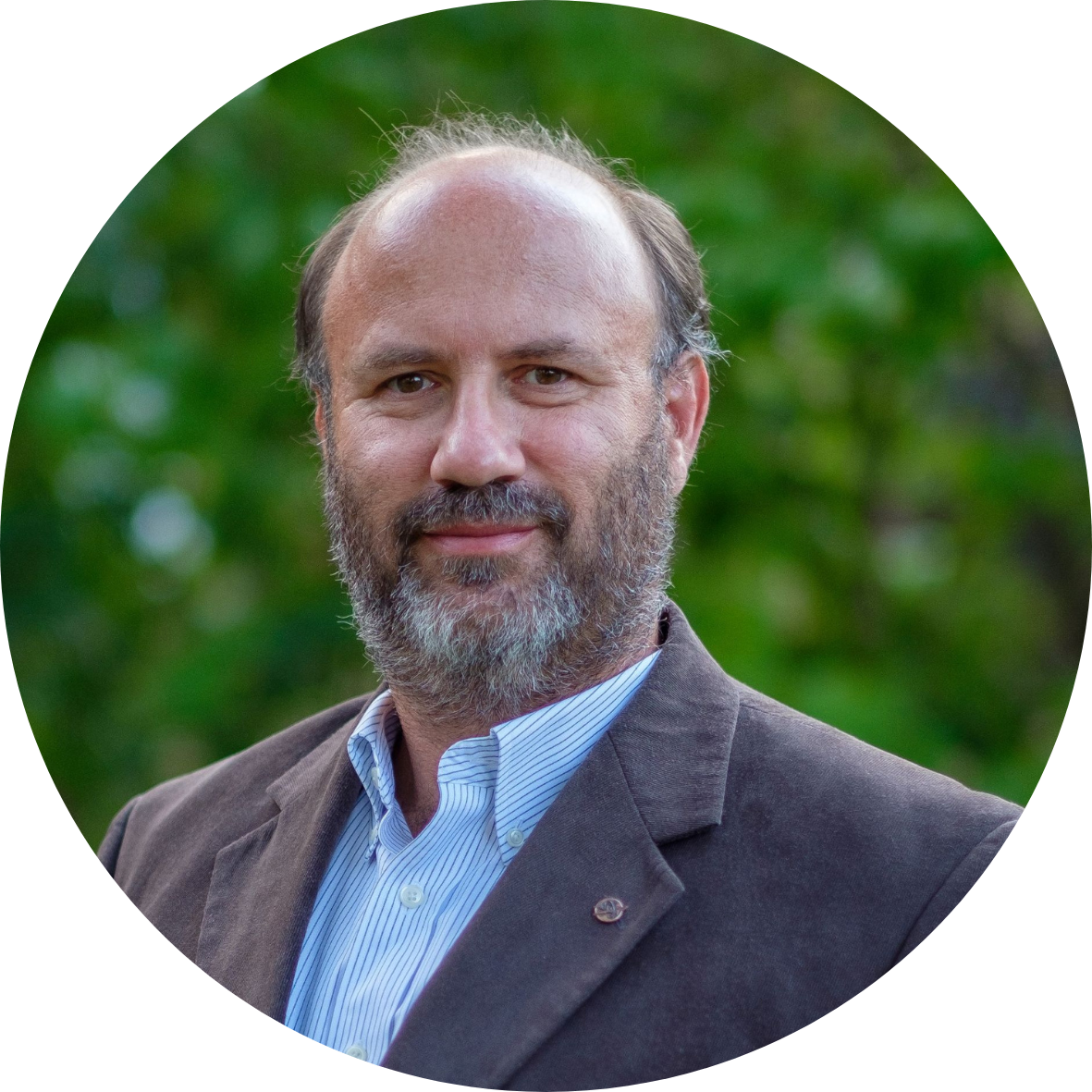
Dr. Andrew Woodworth is currently an Electric Materials Technical Lead for the NASA Advanced Air Transport Technology Project’s Aircraft Electrification subproject, and a researcher in the Materials and Structures Division at the NASA Glenn Research Center. For the project position he advises on a portfolio of work developing multi-megawatt scale powertrain technologies for electricfied aircraft propulsion. Beyond programmatic duties, Dr Woodworth leads a team developing new material approaches for multi-megawatt scale electric machines. He has also been engaged in hardening SiC based power devices to cosmic radiation. Dr. Woodworth earned a Ph.D. in Physics from West Virginia University.
Megawatt and beyond, NASA's Electrified Aircraft Propulsion
Since 2014 NASA has been investing in megawatt (MW) scale electrified aircraft propulsion (EAP). The efforts started with validating the theory that there is benefit in electrification of a transport class aircraft’s propulsion system, and included developing vision vehicles, setting metrics, identifying, and developing key components. Once the concept was validated, work began to elevate the technology to the point of being capable to be used in a flight demonstration system. Three tall poles identified in this development effort were megawatt-scale components capable of operating at altitude, fault management and thermal systems. To that end NASA engaged in further development of components, thermal system development, propulsion controls and upgraded the NASA Electric Aircraft Testbed (NEAT) to test complete multi-MW electrical systems at airplane altitude conditions. This work just wrapped up in 2024 and has had a significant impact on the NASA Electrified Powertrain Demonstrator (EPFD) Project. This impact was achieved though altitude testing of systems and raising the technology readiness level of important components. Recently NASA launched a new effort called High power EAP that focuses on technologies which enable 10+ MW EAP systems. Once again NASA finds itself delving into development of future aircraft concepts and performing early technology development. These efforts will attempt to answer key questions regarding superconducting technology’s readiness to contribute to EAP. NASA has long had an interest in this technology which was included in several early concept vehicles. However, there are significant hurdles to overcome, especially in the development of superconducting electric machines, and the new challenge area will address these head on.
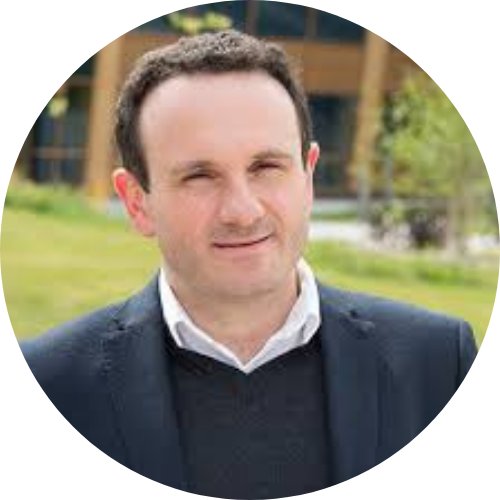
Prof Chris Gerada has over 20 years’ experience in high performance machines and drives. Chris obtained his PhD in Numerical Modelling of Electrical Machines from the University of Nottingham in 2005. Now, Chris is a Professor of Electrical Machines and leads the University of Nottingham's Zero Carbon Cluster of research. His core research interests include design, modelling and manufacture of high-performance electric drives/machines including those for cryogenic propulsion. He leads on a number of MW-class aerospace electric propulsion development projects including high voltage and cryogenically cooled systems and has also lead the development of extensive open-access test and validation facilities. Chris has led several major research consortiums and centers. He’s secured >£100M of research income as Principal Investigator through major industrial, European, and UK grants, and he has a very strong track record of industrial engagement through industrial projects and consultancies. He has published c.700 papers with 10 best paper awards, 2 book chapters, and 6 patents. Chris held a prestigious Royal Academy of Engineering Chair in Electrical Machines, is also the former Chair of the IEEE Industrial Electronics Society Electrical Machines Technical Committee and is an Associate Editor for the IEEE Transactions in Industry Applications. Chris is the recipient of The Grand Nagamori Award (2020) – (Award by Nagamori Foundation – presided by Shigenobu Nagamori – founder of Nidec Corporation) for his contribution to the industrialisation of research.
Electrical Machines and Drives for High Performance Applications